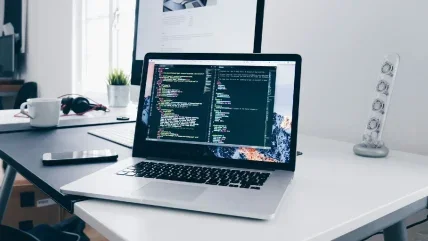
James Watt didn’t invent the steam engine; it was Thomas Newcomen in 1712. Watt just improved it, but it’s his contribution that’s heralded as the dawn of the first industrial revolution. Why? Because Watt made Newcomen’s rudimentary steam process more efficient, efficacious and suitable for industrial use. As any schoolkid will tell you, revolution doesn’t just mean bright ideas, it means their wholesale adoption. It means implementing something so new, so totally, that society gets turned on its head, almost overnight.
The term Industry 4.0, which describes the fourth industrial revolution (4IR), has quietly seeped into tech and manufacturing lingo in recent years. To many, it sounds more like an app update. Before 2020, everybody knew 4.0-associated technologies – AI and machine learning, internet of things (IoT) and data lakes – but not everybody was ready to concede that they amounted to a fourth revolution. Then Covid- 19 hit, sending shockwaves through manufacturing companies the world over. More than just the problems on individual production lines, it exposed the urgent need for greater supply chain integrity. As Amanda Turney, a spokesperson for the FDA, explains, “the Covid-19 pandemic has shown us that the existing manufacturing structures, with a small number of facilities fed by long and complex supply chains, can be disrupted.” In other words, a production line might be manned by sentient robots, but one weak link in the supply chain – as far down as the sixth or seventh supplier – and the whole business might go kaput.
Ian Cronin, project lead for shaping the future of advanced manufacturing and production at the World Economic Forum (WEF), believes that this has brought about a shift in competitiveness. “In the recent past,” he explains, “a supply chain was designed around cost competitiveness. So, how do I get the highest quality product for the lowest price? What we’ve seen in the past 12 months with Covid is the recognition that this needs to be balanced against risk competitiveness. So, you’re not necessarily eliminating those suppliers, or the parts of your supply chain that have the best cost, you just need to be building some resilience and agility into your supply chain, which will allow you to respond when there is a crisis. It’s the idea of distributed manufacturing models.”
The question remains: how do we achieve these distributed manufacturing models? The answer might just be through the implementation of 4.0 technologies. In early 2021, the FDA teamed up with the National Institute of Standards and Technology (NIST) in a bid to “increase US medical supply chain resilience and advanced domestic manufacturing of drugs, biological products and medical devices through adoption of 21st century manufacturing technologies”. As Turney notes, “These include smart technologies, such as artificial intelligence and machine learning, and emerging manufacturing processes.”
All for one
Covid-19 might have brought the need for 4.0 technologies into the open, but the problems the pandemic exposed were as much of an issue three years ago, when the WEF set up the Global Lighthouse Network of advanced manufacturers, as they are today. “The Global Lighthouse Network came about after a WEF and McKinsey & Company white paper emerged, which said most companies that are trying to implement these 4IR technologies get stuck piloting,” Cronin explains. “We realised that 70% of companies never actually end up being able to scale the implementation of these technologies… so, we said, ‘Well, if 70% get stuck, we know that 30% don’t. What if we could identify the 1% who are really doing it the absolute best, where [they have] multiple use-cases at scale and are truly seeing the benefit of these technologies in their production systems?’”
The lighthouses are that 1% from across production sectors – including electronic, automotive, oil and gas, and pharmaceutical – who are leading the way in 4IR. At the time of writing, the latest expansion added 15 new lighthouse factories to the network (making 69 in total), including a Johnson & Johnson consumer health factory in Sweden, the fifth J&J subsidiary in the network and the tenth pharmaceutical or medical product manufacturing site. The beacons are glowing; a revolution, it seems, is growing. As the opening line of the most recent white paper on the Global Lighthouse Network states: “Digital is no longer optional”.
If there’s a lesson to be learnt from these companies, it doesn’t just inhere in 4.0 agility, but in the seismic shift being seen across sectors, companies, and institutions towards better communication and collaboration. “I know that’s not necessarily a techy response,” Cronin admits, “but what we are seeing is that you can become more innovative, more efficient, more sustainable, if you can figure out different models of actually engaging with data across the players.” Unsurprisingly, there’s been resistance to this in the past. For a long time, as Cronin observes, “companies were afraid to do that because of IP reasons, but the technologies themselves are allowing you to protect your data while also sharing things that are mutually beneficial.”
The result is technological homogenisation across different industry sectors – which is, in part, what makes 4.0 such a revolutionary turn in manufacturing history. It’s why the WEF created the Advanced Manufacturing and Production community and platform. “Traditionally,” Cronin explains, “people had thought about vertical industry sectors – I’m in the aerospace sector, I’m in the automobile sector – but what we realised was that the technologies that are impacting manufacturing are sector agnostic.
“[And when it comes to] other global trends that are impacting supply chains – whether that’s geopolitical and trade realignments, or climate change – it doesn’t matter what sector you’re in and so the technologies are transforming across industries.”
Talking therapies
Kelly O’Brien, assistant lecturer and researcher at Limerick Institute of Technology, echoes Cronin’s notion of sector agnosticism. “It’s very exciting from the research point of view,” she says, noting the use of virtual and augmented reality technologies, which many believed were purely for entertainment, to train manufacturing staff. “We’re talking about technologies that we all know so well, but applying them in very different ways.”
O’Brien has been working on a research project that looks at how the academic sector can help SMEs to get on to the 4IR ladder. Like Cronin, she also stresses an urgent need for collaboration and transparency. “It has very much been the case,” she notes, “that there is research going on in the colleges that has nowhere to go and there are companies that have the money to spend, but they’re not sure how to spend it.” The collaborative model that she outlines is different to Cronin’s – focused instead on connecting industry and academia – but the point remains the same: people need to start talking.
It does seem like an unusual response from the tech industry, and a surprisingly human one in a topic centred around AI. Then again, if Covid-19 has revealed anything, it’s that if we don’t learn to communicate now – whether that means supply chain transparency or keeping in touch with distant relatives – then perhaps we never will.
The collaboration between the FDA and NIST was born out of the Covid-19-triggered revelation that supply chains can be disrupted; but it recognises that there’s more to solve than the pandemic. “The FDA and regulated industry have to accelerate the adoption of advanced and smart manufacturing technologies to strengthen the nation’s public health infrastructure,” Turney explains.
As one example of the technology being developed out of the collaboration, Turney offers the modularised process, which “entails breaking manufacturing down into parts that can be plugged into each other and still function, much like train cars can connect to any engine”. Modularised processes make it possible to switch production from one pharmaceutical or regenerative medicine product to another, in days or hours, using the same facility. It might be a 4.0 technology, but without communication, transparency, and cooperation, it would be just another bright idea. It’s Watt’s steam engine all over again – existing technologies being adopted, altered, repurposed and modulated to change the manufacturing process for good. And over this new revolution, Watt’s train car still presides; that material archetype of industrial innovation haunts even the most ephemeral of modern manufacturing processes.
10
Pharmaceutical and medical product manufacturing sites in the WEF advanced manufacturing lighthouse network.
WEF