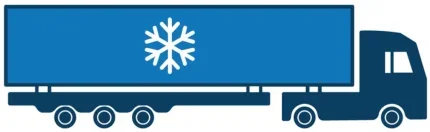
Over the years ahead, the pharmaceutical cold chain industry will have a mammoth task on its hands. For one thing, supply chains are becoming more complicated. With drug production frequently being moved to emerging markets, far away from the end users, the cold chain may involve long journeys and multiple transport modalities. Potentially, this comes with a higher risk of temperature deviations.
The molecular makeup of drugs is changing too. According to IQVIA, drugs requiring cold chain storage and distribution comprised 26% of the pharmaceutical market in 2017. By 2022, it was 35% – and with over half of new medicines falling into this bracket, that proportion is likely to grow further still. Of particular note are cell and gene therapies, which need ultra-frozen storage (at -180C and -80C respectively). This is far lower than the 2–8C that most drug products require.
Against this backdrop, we are seeing strong demand for cold chain services that can reliably preserve the medicine. Quality will always be the top priority for the cold chain industry, driven by good manufacturing practice (GMP) and good distribution practice (GDP) guidelines.
Unfortunately, ensuring quality may sometimes clash with another big imperative – to keep driving towards sustainable goals. Take the expanded polystyrene (EPS) containers that are traditionally used for deliveries, in conjunction with frozen gel packs. While highly effective, this solution is wasteful as the containers cannot be reused.
“It’s often very possible to comply with GMP while being sustainable,” comments Tom Rose, SVP of clinical trial sourcing at Clinigen. “However, the issue is keeping the cost down. We need to use emerging technologies to keep down the cost of supplies, so that manufacturers are incentivised to make more sustainable materials without putting the cost onto the patients. And the same goes for GDP – going forward we must comply with an eye on reducing our carbon emissions.”
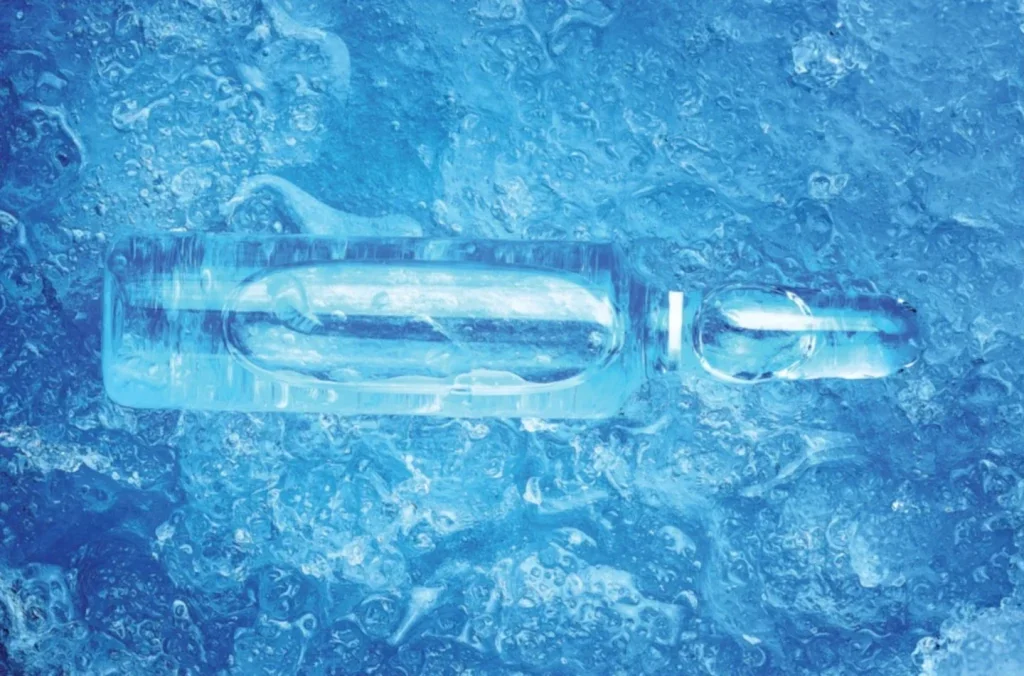
The drive towards sustainability isn’t necessarily fuelled by regulatory pressure. But with plenty of voluntary initiatives in place, companies are interested in making changes both from a reputational and ethical perspective. Many have made firm commitments towards carbon neutrality, and minimising their footprint in the supply chain is a large piece of the puzzle. Any third-party logistics providers they choose to work with will need to share those sustainability goals.
Clinigen, for its part, has set a Net Zero ambition for 2040. As part of this, the company is looking to obtain Science Based Target Initiative (SBTi) approval for all its environmental goals by 2025.
The need for change
As Rose reinforces, while quality and sustainability don’t need to be at odds, meeting both goals simultaneously ‘isn’t an easy ask’. Given the sheer length of the cold chain, and the number of steps and handovers along the way, it may require an entire systematic transformation.
“From the manufacturer to in-licensor to wholesaler, to the packaging and distribution players and finally to patients, there are various points of pick-up and drop-off that need to reach and maintain sub-ambient temperatures,” he says.
On top of that, product requirements vary significantly. Some need specialised packaging materials, which may not be as environmentally sound as one might wish. After all, if certain materials are used for only one niche, the industry is less likely to spend the time moulding them to the latest standards.
The upshot is that driving positive change across supply chains will require an influx of new ideas. Everyone involved in the process – manufacturers, suppliers and distributors – will need to take advantage of new technologies, which can help them meet quality and sustainability goals without expending unrealistic resources.
“If a product is high quality and its supply chain has a reduced carbon footprint, but is at a cost that is prohibitive to its equitable access, then this isn’t a sustainable solution – nor a solution at all,” points out Rose.
Optimising journeys
So, given the scale of the challenge, what can the cold chain industry do in practice? The most cost-effective way to reduce its carbon footprint might also be the simplest – namely to shorten the journeys taken. This doesn’t have to mean re-siting manufacturing facilities nearer to the enduser; it can also mean planning the transit route more effectively.
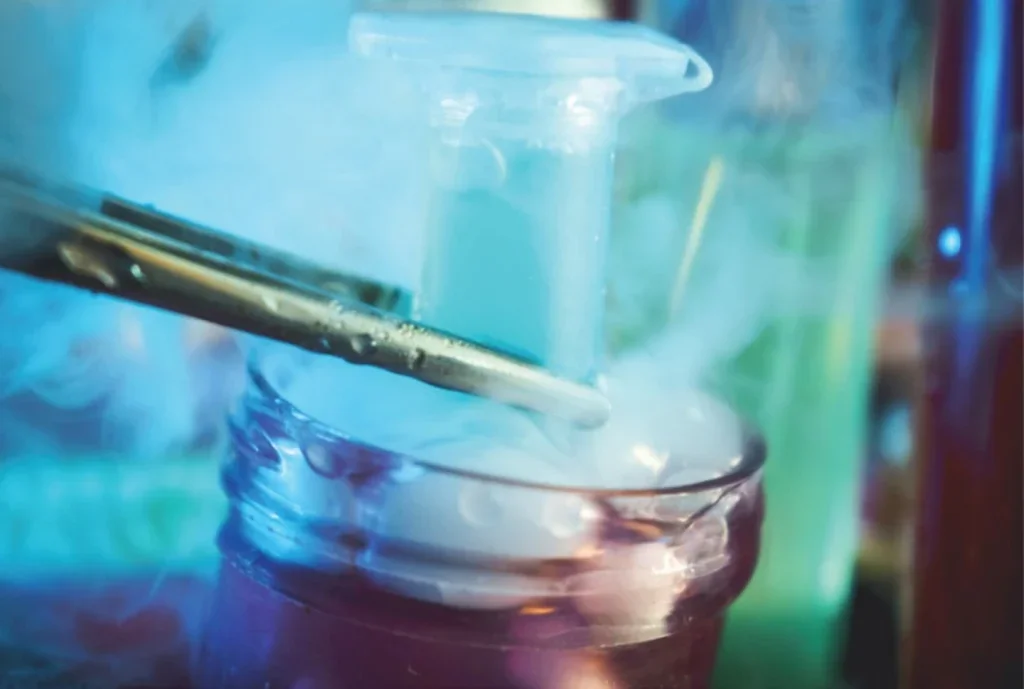
“Creating a shorter path that requires fewer stopoff points – or anything that reduces the amount of transit via land, sea and air – can significantly reduce its impact on the environment,” says Rose. “This can be done by using combined services that pack, label and distribute in one, consolidating what would be multiple stops on the supply chain. Similarly, procurement direct from the manufacturer would avoid routes through wholesalers or other intermediaries and can reduce the stops the product takes.”
Another option might be to switch from air freight to sea – or at least, achieve a better balance between the two. According to the MIT, for every ton-mile travelled, air freight generates 47 times more greenhouse gases than ocean shipping.
“Quality and sustainability don’t need to be at odds, but meeting both goals simultaneously isn’t an easy ask.”
What’s more, as many as 20% of temperaturesensitive medicines are impacted by temperature excursions during air freight. While ocean freight is considerably slower, this may be offset by cost and sustainability gains. It may also bring greater scope to address temperature deviations in real time.
As for the land portion of the journey, some big pharma companies are investing in fleets of electric or hybrid vehicles. AstraZeneca, for instance, says that over 50% of its fleet is now electric, and that the electricity used will be fully renewable by 2025.
35%
The percentage of the pharmaceutical market that cold chain drugs comprised in 2022, up from 26% in 2017.
IQVIA
“The use of electric vehicles (EVs) is still limited but is increasingly becoming a factor in making the cold chain industry more environmentally friendly,” says Rose.
Many pharma companies choose to outsource their cold chain services to specialist providers, which have a strong track record in optimising shipping models and balancing environmental concerns with the need for speed.
Reducing waste
Another important strategy for mitigating climate impact is by reducing waste – both in terms of product waste and packaging waste. The former, says Rose, can be addressed with better inventory management and forecasting solutions.
“If a product is high quality and its supply chain has a reduced carbon footprint, but is at a cost that is prohibitive… then this isn’t a sustainable solution – nor a solution at all.”
“Forecasting clinical trials is a difficult task as there are many variables that arise or change throughout the process, but it’s critical to the management of supplies and reducing waste,” he says.
Over the next few years, we will start to see many of these forecasting processes automated using new digital tools, such as AI and machine learning. These tools, thinks Rose, will be key for the overall reduction of waste, as well as providing alternative methods for product movement through the market.
50%
The percentage of AstraZeneca’s fleet that is now fully electric, with plans to use 100% renewable energy by 2025.
AstraZeneca
Clinical trial sponsors will be able to run through all possible scenarios ahead of time, for instance modelling what might happen if enrolment numbers or study resources change. This will help them ascertain what kinds of goods and materials they might need, and when they might need them – critical considerations for boosting the sustainability of a trial.
47x
Air freight generates 47 times more greenhouse gases per ton-mile than ocean shipping.
MIT
Similarly helpful for reducing waste is the real-time monitoring of stock. For instance, companies might use special sensors, enabled by the Internet of Things (IoT), to keep track of products as they move through the cold chain. Logistics providers can receive notifications whenever any temperature deviations occur, giving them a better chance of remedying the problem. Data can be logged automatically, and retrospective analyses performed.
Packaging waste can be minimised not only through better inventory management, but also through changing the materials used. Rose notes that Clinigen uses reusable packaging materials for all its shipments, reducing the carbon footprint that comes from destroying old materials and creating new ones.
“Packing materials are in a constant state of evolution – to meet demand, packagers are having to switch between the safest and most costeffective packaging,” says Rose. “However, it’s more crucial than ever that packages also follow specific environmental standards. All packing in the future must be reusable packaging, while sustaining a safe temperature for up to 160 hours outside of a refrigerated space.”
For instance, many logistics providers are now packing their temperature-sensitive products with vacuum-insulated panels and Phase Change Material (PCM) based coolants. Both parts are reusable: the vacuum-insulated panels can be used efficiently for more than five years, and the cooling elements for an indefinite basis.
Taken together, the packaging can maintain the temperature set point for several days or even as long as a week. Because it doesn’t require an energy source, unlike traditional refrigerated containers, it creates no emissions when in use. And while high-performance solutions of this nature are expensive to purchase, that cost needs to be offset against the likely gains.
It’s clear that boosting the sustainability of the cold chain structure, while a challenging task, is more than achievable with the right kind of mindset shift. However, Rose goes on to caution that environmental considerations should never be a valid reason to complicate or overprice the cold chain.
“What many suppliers are most concerned about is that these sustainable changes are economically viable for the future, and don’t pass on added costs to patients,” says Rose. “This could reduce patients’ access to medicine, a side effect that the global population can’t afford. We must challenge ourselves across the industry to both increase access and sustainable standards in one go.”