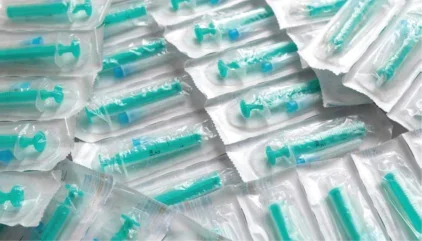
As one of many crucial processes in the pharmaceutical and biotech industries, container closure integrity testing (CCIT) plays a pivotal role in confirming that container closure systems (CCS) will keep products viable for use. Not only is patient safety at stake, as contamination with air, moisture, and microorganisms could severely impair the efficiency of drug treatments, but pharma companies could lose valuable batches of medicines or vaccines.
The scope of CCIT has greatly expanded over the years, and because defects in pharmaceutical packaging components are not always obvious to the naked eye, many different methods have evolved to find even microscopic cracks in glass vials or subtle defects in elastomer stoppers.
“You are protecting the product from the environment, and the environment from the product,” says Christian Proff, senior verification engineer at Hoffmann-La Roche. “Some medicines are highly toxic, including cancer drugs, so you don’t want them to end up in a toddler’s hands.”
“Mainly, the focus is on the safety of the drug substance, making sure it is not being diluted or contaminated, particularly if the drug is injected, as it bypasses most of the body’s defence mechanisms,” he adds. “If something gets in that can survive or proliferate, then drugs could potentially become a deadly threat.”
Companies have long relied on probabilistic methods like microbial challenge, bubble emission, tracer gas detection, and blue dye ingress. All have their merits, but they provide subjective outcomes. Now, more deterministic methods, such as vacuum decay, pressure decay, headspace gas analysis, and vacuum deflection by laser measurement are often preferred. They are non-destructive and provide more objective measurements of leakage.
“A series of statistical events has to take place to give a positive readout for ingress, so there is a chance you can test a bad sample and not see the defect, which means you must test a large number in order to properly assess the risk of failing integrity,” Proff explains. “Microbial ingress is a probabilistic method as per US Pharmacopeia (USP) chapter 1207, which gives you a yes or a no – a qualitative answer – while physical test methods are generally deemed as deterministic, and provide quantitative results.”
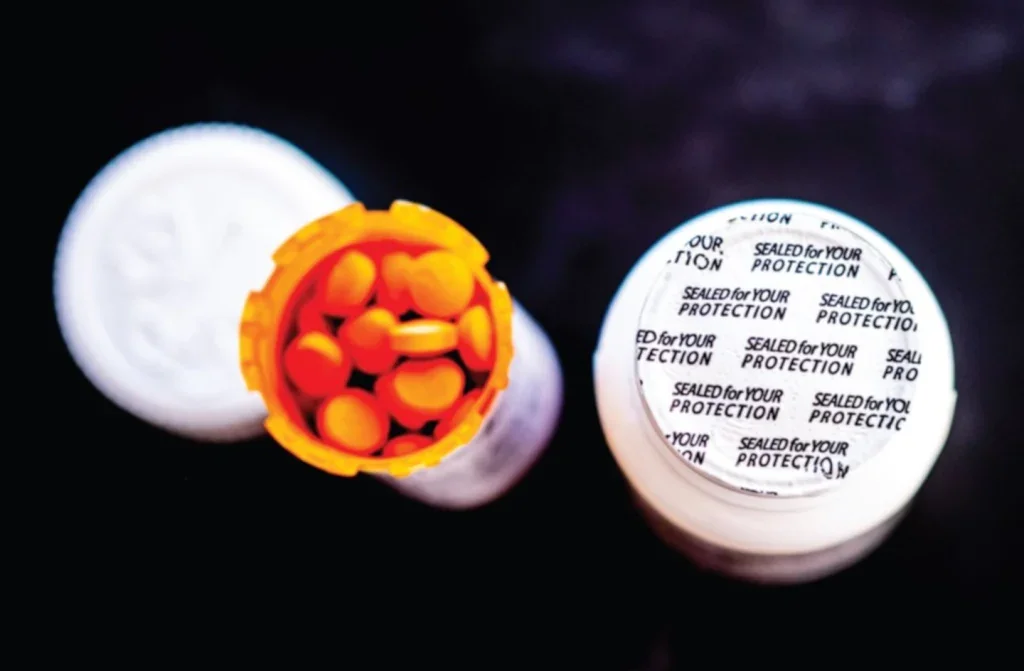
Deterministic test methods rely on physicochemical technologies. In contrast, results of most probabilistic tests are visually assessed, so any variation in the skills of the technician can impart bias. In a dye test, for example, which relies on seeing a colour, the human eye may not provide consistent results.
“Methods providing a qualitative output are inferior to quantitative methods“, adds Proff. “This is like measuring people’s height as under or over 170cm, compared to measuring and noting everyone’s height individually to get a representative sample and seeing the complete height distribution. Knowing the distribution enables me to better judge how many units I need to test and how good they have to be in order to suggest a whole batch is defect-free.”
Pros and cons
Choice of test clearly depends on the drug and the container. For a drug substance that is sensitive to oxygen, gas tightness is a key issue.
“Everything depends on the formulation, so you have to consider the content,” says Proff. “There are some techniques that are more practical for increased sensitivity levels, such as headspace analysis, but you might have to wait longer with exposure to the tracer gas to see smaller defects.”
Headspace analysis is a non-destructive, laser-based, and fully automated inspection method for sealed drug delivery solutions. By assessing the partial pressure of a given gas molecule in the area inside the container that does not contain the product itself – the headspace – it measures the quantity of specific gases and how their composition changes over time. This determines whether a gas can permeate the CCS.
Helium leak testing is another common CCIT method. It involves either adding helium inside the container before closure or purging the container with helium on the atmospheric side of the test with leakage being detected on the vacuum side by an increased helium signal. One advantage is that it is highly sensitive and can detect even the smallest of leaks. Also, it has essentially the same test duration no matter the size of the defect of interest.
“Helium is an ideal tracer gas, as it is a noble gas, which will not react with any matter in the container and therefore lead to immediate detection upon leakage,” says Proff. “There are very low levels of helium in the atmosphere – around 5ppm – so you can be sure that the helium you introduce to the test system is generating most of the signal. That would not be the case with oxygen, carbon dioxide, or water under normal circumstances.”
Nevertheless, helium is not everyone’s preferred choice. Its use can be more cumbersome to automate than other substances, and there is scope for false positives. Laser-based headspace scores higher when it comes to ease of use. Another complicating factor is that the limited global supply of helium makes it expensive. High voltage leak detection (HVLD), also known as the conductivity and capacitance test, is another technique for leak detection in non-porous, rigid or flexible packaging containing liquids. Using the principle of electrical conductivity and resistance, voltage and detection probes are positioned on either side of a rotating sample to scan the geometry of the package. In a non-leaking package, the current emitted by the voltage probe will register as a low voltage in the detection probe. If there is a leak, capacitance on one side of the packaging will be eliminated, so a higher voltage will register.
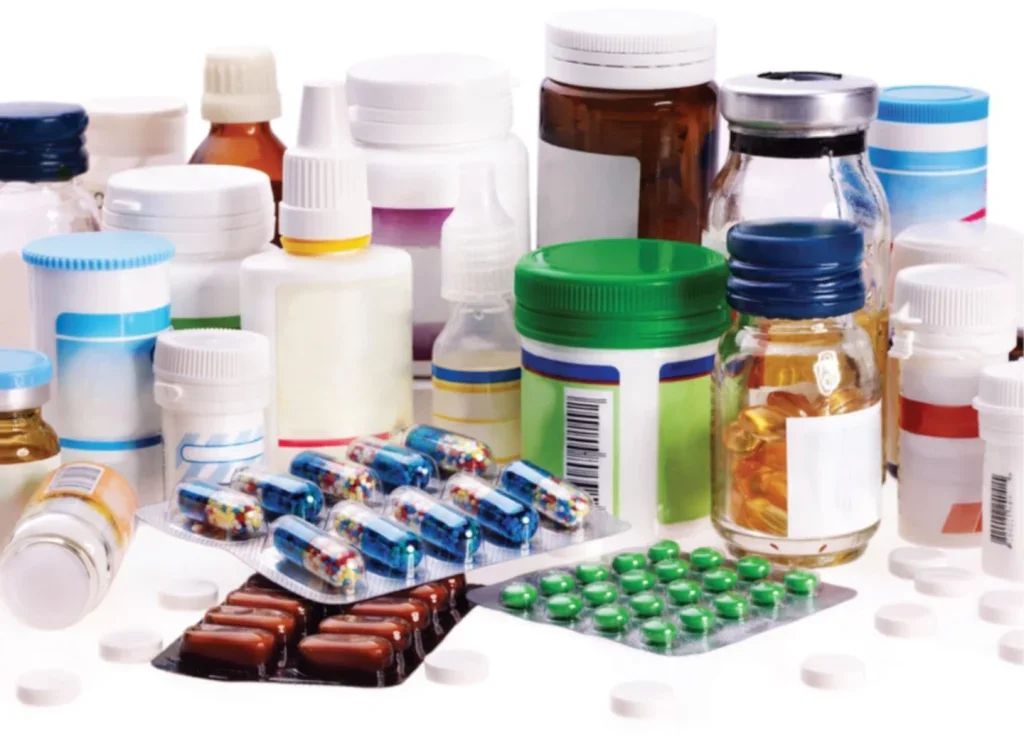
Every process for CCIT also has to contend with the fact that drug containment and delivery systems are increasingly complex and intricate, often consisting of many components and a variety of materials. The need to ensure that all components are rigorously tested is a complicating factor.
“In the case of syringes and cartridges, which have a movable stopper, problems can arise because you usually do not want to move the stopper during testing, as this alters the system one wants to characterise,” says Proff. “Pre-filled syringes or cartridges are both devices and primary packaging in one, which is not the case for a vial. Devices often come with an added complexity due to the several functions one component has in this combination.”
“There are many criteria that determine test method selection,” he adds. “Are you using flexible or rigid packaging? Rigid packaging will not deform with pressure, but flexible packaging will. In a vial that has been closed there are no movable components, but the stopper in a syringe must move. Glass is not permeable to gas, but polymers will typically exhibit gas permeation over time. And with metallic materials, electric conductivity could lead to issues with tests identifying defects based on local changes in conductivity such as HVLD.”
The burden of choice
Overall, helium has one major advantage. Sample preparation is cumbersome, but the sensitivity level is high. But every CCIT technique has pros and cons, so there is no clear way to say that one is always preferable.
“So what do you optimise for?” asks Proff. “If you need to test lots of samples then perhaps use headspace, which can use an automated conveyor belt to present and test individual samples, one after the other, at very high speeds in on-the-market available configurations. The throughput is huge, so you could test an entire batch. Using helium means throughput is dramatically lower, but you extract potentially way more information regarding the performance of the CCS, which renders it very useful in CCS development to characterise a system’s properties with high sensitivity and short test cycles.”
The key is to understand early on the key risk criteria and develop a plan for CCIT along with the development of the product and the packaging. After all, different technologies see different things and identify different issues.
USP 1207 Package Integrity Evaluation – Sterile Products lists the recommended CCI testing methods for primary containers of sterile dosage forms. The last iteration was released in 2016. More recently, the European Union released the GMP Annex 1, which came into effect in 2023, mandating the use of a ‘statistically valid sampling plan’. This dismisses visual inspection alone as an acceptable test method, so more sophisticated CCIT methods are now required.
“Testing must be considered right at the start of the development of the product,” stresses Proff. “You shouldn’t leave that decision to a late development stage, though that can happen. You must consider this as a priority task on the action item list early on, to define the best-suited CCI test method depending on product requirements and available packaging solutions, and if necessary change to more appropriate ones throughout the development process.”
Late-stage CCI test failure in development could lead to a massive delay on the path to marketing approval. Whatever method is ultimately preferred, do not leave the choice to the last minute.