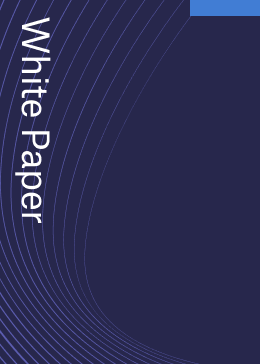
Software suite lays down the tracks for compliance
By Mettler-ToledoMettler-Toledo is a leading global manufacturer of precision instruments and services, for use in laboratories and manufacturing. Reinhold van Ackeren, head of...
Read more
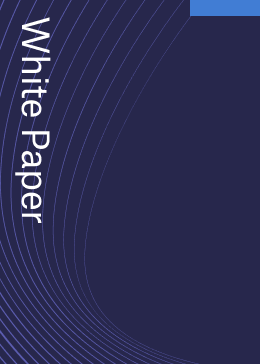
A leading resource for the Pharmaceutical industry since 2002
Mettler-Toledo is a leading global manufacturer of precision instruments and services, for use in laboratories and manufacturing. Reinhold van Ackeren, head of...
Read more